金属加工刀具在人类历史的进步与发展中占有重要的地位,在18世纪后期,伴随着蒸汽机等机器的出现,工业用刀具才得到了快速的发展。随着现代工业的突飞猛进,刀具在各行各业中发挥着极其重要的作用!
近10年来,作为高端制造的重要利器,国产金属加工切削刀具取得了重大的技术进步,为我国航空发动机制造水平的提升提供了强有力的支撑。
航空发动机零部件中的涡轮盘、风扇盘等盘类零件,通常具有榫槽结构,以便于安装叶片。榫槽沿零件的外径分布,呈圣诞树形状,不仅结构和空间角度十分复杂,而且对加工精度和表面粗糙度的要求极高。
此外,航空发动机零件所用材料通常为高温合金和钛合金等难加工材料,这进一步增加了加工榫槽的难度。因此,针对拥有榫槽结构的盘类零件加工,航空发动机制造业普遍采用拉削技术来提高加工的精度和效率,这使得拉削刀具在航空发动机制造领域具有不可替代的重要作用。
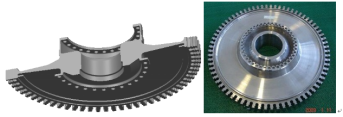
带榫槽的航空发动机零件
长期以来,加工带榫槽结构的盘类零件所用刀具通常为高速钢拉刀,这类刀具在加工高温合金和钛合金材质时寿命较低,需要经常换刀才能满足拉削精度要求,但每次换刀都要经历复杂又费时的调试过程,从而极大地影响了生产效率。因此,航空制造企业迫切需要使用寿命更长且更换刀片更便捷的新型拉刀产品。
针对航空发动机制造业加工盘、环、轴类零件的需求,株洲钻石切削刀具股份有限公司(简称株钻)与中国航发动力股份有限公司(简称航发动力)紧密合作,采用国产硬质合金牌号,成功地开发出硬质合金开槽拉刀和倒角拉刀。
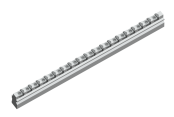
开槽拉刀
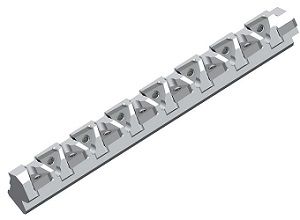
倒角拉刀
通过对带榫槽结构的钛合金和高温合金盘类零件进行拉削加工试验,结果表明:与高速钢拉刀相比,株钻与航发动力合作开发的硬质合金拉刀具有更高的加工稳定性,使用寿命更长,减少了换刀次数和调试刀具所占用的时间,提高了生产效率,最终降低了生产成本。
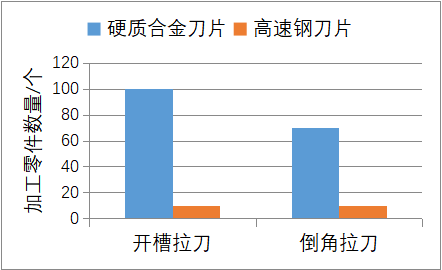
钛合金TC11榫槽拉削加工对比
目前,硬质合金拉削刀具在国内外刀具市场中较为罕见。株钻与航发动力紧密合作,经过反复的参数修正、不断的装夹和切削试验,最终优化并完善了刀具的各项性能参数。
试验验证表明,新开发的硬质合金拉刀在加工精度、使用寿命和加工效率等方面均较上一代拉刀具有明显的优势。
同时,该刀具在结构设计上具有创新性,获得了两项发明专利授权,已在航发动力得到推广应用。
来源:工业智慧院