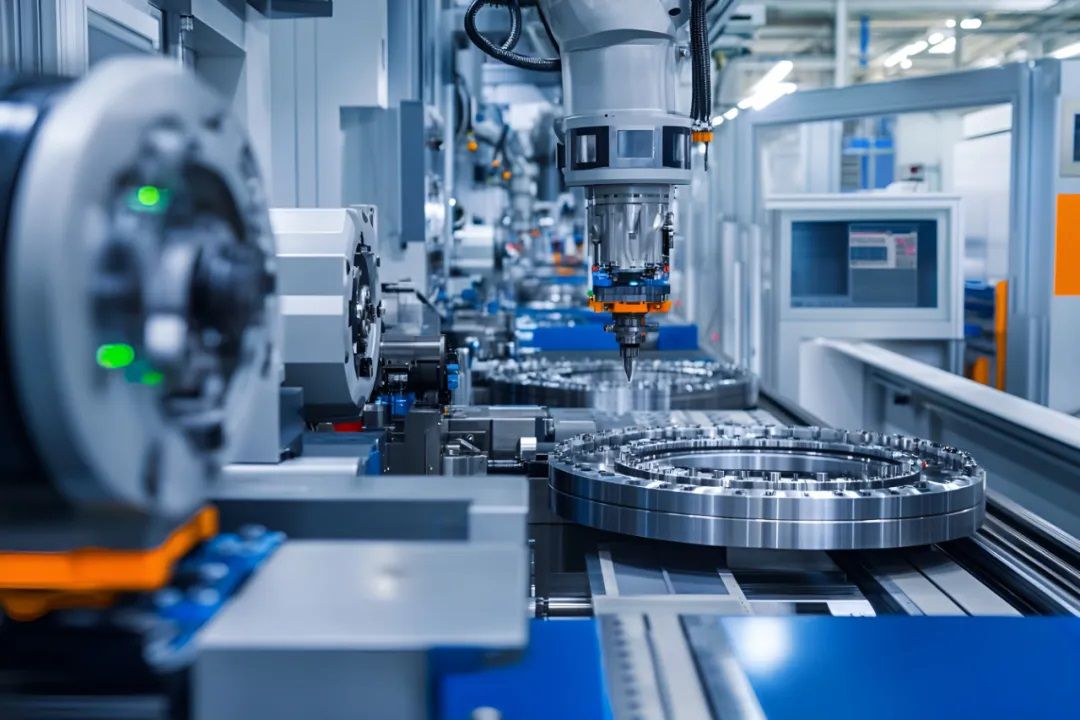
作为机床界的顶级盛会,CIMT2025中国国际机床展览会以总展出面积达31万平方米,一举创下近十年全球机床工具展会规模之最。中国机床企业在本次展会上推出了一批具有自主知识产权的新产品、新技术,成为展会上一道亮丽的风景线。从曾经的“仿制”模式,到如今逐步迈向“创新驱动”阶段,国内企业的转型升级之路走得坚定而有力。部分产品在功能、精度等核心指标上已与国外展品并驾齐驱,甚至实现超越,表明我国机床行业发展取得的阶段性新突破,中国机床行业也正从“跟跑”向“并跑”“领跑”加速迈进。
然而,在看到成绩的同时,我们也要保持清醒的头脑。我国机床行业仍面临诸多挑战,核心技术攻关能力有待进一步提升。行业上下游需加强协同创新,形成强大的发展合力,持续抢占行业发展制高点。
高性能、复合、智能、绿色节能成主旋律
在制造业加速变革的当下,机床作为制造业“工业母机”,其发展方向备受关注。CIMT2025中国国际机床展览会展现出机床行业高精、高速、高效、复合化、智能化、绿色节能化等发展趋势。
展会上,国外展商纷纷亮出“看家本领”,在高精、高速、高效方面展现强大硬实力,重复定位精度±0.8μm,加工精度±1μm,表面粗糙度达Ra0.01μm,相当于头发丝的1/8000;快速移动速度达120米/分钟,加速度可达1g,大幅提升加工效率和节拍。多轴联动、车/铣/磨复合、增减材复合等多种复合形式产品不断出新。国外展商展品通过集成多轴、车、铣、磨、电加工多种工艺复合形式,一次装夹即可完成复杂零部件全工序加工,有效减少了装夹误差和工序转换时间,推动加工制造向集约化、柔性化发展,提升了复杂零件的加工精度和效率。
以国外数控系统龙头企业为典型代表,推出智能数控系统、自适应加工技术、预测性维护解决方案等创新应用,推动机床设备从自动化向自主决策、智能调控升级,有效提升了生产效率和产品质量稳定性,为制造业数字化转型提供了有力支撑。
随着“双碳”目标的深入推进,绿色节能技术也成为机床行业竞争的新焦点。高效节能电机、切削液循环利用装置、智能能源管理系统等绿色制造技术广泛应用,机床设备能耗显著降低,切削废料回收利用率大幅提升,绿色设计、低碳工艺等理念贯穿产品全生命周期,推动机床行业向资源节约型、环境友好型转型。
国产机床比肩国际巨头
国产机床设备在高性能、复合化、智能化等关键指标上实现重大突破,与进口设备的差距日益缩小,部分指标甚至实现反超,为我国机床产业迈向中高端水平注入强劲动力。
国产机床在精度控制技术领域持续深耕,取得显著成效。通用技术机床研究院展出的UPT250B超精密单点金刚石车床主轴回转精度小于30nm,直线运动轴定位精度小于0.3μm,重复定位精度小于0.2μm;浙江博谷智能的超精密以车代磨硬车削机床主轴回转精度小于0.1μm,直线运动轴定位精度小于1μm,重复定位精度小于0.2μm,展现出国产机床的强大的精度实力。
在超高速加工上,国产机床同样表现亮眼。广州昊志在展会上发布的国产首款10万r/min超高速电主轴,填补了国内空白,为我国超高速加工技术发展提供了有力支撑。上海拓璞展出的超高速五轴龙门加工中心,通过复合材料、直线电机、智能补偿等先进技术,实现了轻量化节能,快移速度高达120m/min,超高精度五轴龙门加工中心快移速度也能达到80m/min。
山东大汉智能科技的HTMC800T摆头车铣复合机床,定位精度达到±3μm,重复定位精度±1μm,在复杂曲面加工领域,精度表现足以与进口设备相媲美,为航空航天、精密模具等对精度要求极高的行业提供了国产装备新选择,打破了国外设备在该领域的长期垄断。
面对制造业对复杂零部件加工效率和精度日益增长的需求,国产复合化机床也不断创新突破。济南二机床的新能源汽车大型一体化铝合金压铸零件加工智能生产线,为新能源汽车行业提供定制化解决方案。它由1台高速双龙门五轴加工中心和1套机器人自动上下料物流系统组成,加工中心采用整体式床身与大型直驱翻转工作台,配置自主研发的偏置式B/C双摆角数控万能铣头,工作台最大翻转直径Φ2200mm,双主轴最大间距3300mm,最大快移速度120m/min,主轴最高转速20000r/min,刀库换刀时间≤3s,X/Y/Z轴加速度0.7/0.7/1.3g,可一次装夹下完成新能源汽车前机舱、后底板及电池壳等大型一体化铝合金压铸零件的多工序加工,有效减少了装夹误差与工序转换时间,极大提升了加工效率与精度,为新能源汽车产业发展提供了有力保障。
山东豪迈机床的五轴超快激光微加工机床LTM55,集成了“激光+切削”复合工艺,巧妙解决了传统纯激光加工的表面粗糙度问题,在高精度与高效率方面已具备与国际先进水平竞争的实力,为我国微加工领域的发展开辟了新路径。
这些复合化设备的涌现,表明我国机床产业在复合加工技术领域正逐步打破国外在该领域的垄断,为我国制造业高质量发展注入新动力。
随着人工智能、大数据、物联网等新一代信息技术与机床产业的深度融合,国产机床智能化水平也实现了跨越式提升。
华中数控发布的全球首台具备自主学习能力的智能数控系统“华中10型”,通过“1+2+3”创新架构,即1个智能底座、2条数字主线、3大智能子系统,实现了机床从“被动执行”到“主动决策”的转变。其内置的DeepSeek大模型能够实时优化加工参数,将复杂零件编程时间从人工半小时大幅缩短至3分钟,加工效率最高可提升20%,大大提高了生产效率,降低了生产成本。
武重集团推出的高速高精智能重型立式铣车加工中心,依托“武重云”工业互联网平台,深度融合人工智能、数字孪生及大数据技术。通过自主研发的智能数控系统和多维度传感器网络,实时采集设备振动、温度及能耗数据,构建动态数字孪生模型,实现加工精度自主优化与故障预判。其AI诊断模块可提前识别刀具磨损、部件老化等风险,主动触发维护程序,将故障响应时间缩短至分钟级,维护周期优化超30%,有效提升设备综合效率(OEE)达40%,为重型机械加工领域的智能化转型提供了成功范例。
这些成果充分表明,国产机床在智能化方面已具备与进口设备一较高下的实力,为制造业数字化、智能化转型提供了有力支撑,助力我国从制造大国向制造强国迈进。
欣喜背后的隐忧
国产机床诸多亮点的背后,行业长期积累的深层次问题依然存在,成为国产机床迈向高端市场的“绊脚石”。
从CIMT2025展出的国产高端产品整体情况来看,可谓品类齐全、规格多样全面,在精度等性能方面也不输国外展品,完全具备服务高端制造业的实力。但由于缺少新的技术赛道,国外机床产品仍然具有较高的技术门槛和市场门槛,国产机床新技术和新产品推出较晚,缺乏充分的评价和市场化应用,在市场推广时,依然存在不同程度的“信任危机”。
主机企业对数控系统及核心、关键功能部件“不敢用、不愿用”,用户企业对主机也持类似态度,市场信任度较低。在航空航天、汽车、集成电路等高端领域,涉及高精度、高一致性加工时,国产机床在加工效率、精度持久性、可靠性、稳定性方面暴露出的部分不足,使得即便有技术新突破,也因未经过足够的实战检验,难以获得客户的充分信任,市场拓展之路困难重重。
我国机床企业工艺综合服务主要侧重在生产产品的关键件加工工艺、产品组装工艺以及与生产质量相关的工艺装备等方面,对客户的应用需求关注不够,不能高效、精准为客户提供含厂房规划、人流及物流流转、设备布局、用户零件加工工艺、信息化等全流程、全套工艺服务解决方案。
这种情况下,既无法满足客户的多样化需求,也不利于根据客户需求快速进行产品迭代升级和新品开发。在与具备全面综合服务能力的国际企业竞争时,我国机床企业明显处于劣势,不利于在高端市场的应用和拓展。
国产机床在CIMT2025机床展上的出色表现,让我们看到了其崛起的希望。但要真正实现抢占高端市场,还需提升自身技术实力、工艺综合服务能力和加速产品中试验证,提升市场信任信心,在与国际机床巨头市场竞争时,国产机床才能站稳脚跟,抢占一席之地。
机床产业的突围
作为制造业的“工业母机”,机床技术水平关乎着国家安全战略与制造业的核心竞争力。然而,长期以来,我国机床产业深陷基础共性技术薄弱、高端技术过度依赖国外的困境,尤其在高端数控机床领域,与西方先进水平存在明显差距。
在当下全球局势风云变幻、制造业深度变革的大背景下,机床行业的自主可控已刻不容缓,而协同技术创新则成为突破困局、跨越技术壁垒的关键路径之一。
技术创新不应是一句口号,而是需要业界同仁齐心协力、锚定方向、重点攻关、持之以恒,要有不达目标誓不罢休的决心。既要重视基础共性技术的深耕细作,也要掌握能一招制敌的“杀手锏”技术,同时还要狠抓应用技术的突破。
一是在推进技术创新的同时加强产业政策的匹配。通过项目驱动建立良好合作关系的基础上,推动建立高端产品国内采购、国产化比例等制度化要求,为机床企业高端产品研发制造提供稳定预期;借鉴“预先研究-技术应用-型号研制”体系的经验,面向重点领域新产品研发的技术需求、共性应用基础技术开展“同步预研”,避免分属于应用基础研究、应用技术、工程化不同科研阶段的技术问题“胡子眉毛一把抓”,解决国产高端机床的创新源头问题;推动创新型产品、数字化技术应用的标准研究,发挥我国信息技术优势,为机床行业创造“新赛道”超车机会;在进出口及招投标等政策上与创新政策趋同,共同推动高端机床、数控系统和功能部件的批量应用。
二是加强机床产业链跟踪监测和产业创新数据分析。针对机床领域产业、科技信息数据统计不充分、失真的突出问题,应对标世界先进,动态收集、分析国际、国内机床科研、技术、企业等相关信息,跟踪正在出现的连续性或者非连续性专业技术变化,掌握现有和潜在竞争对手的能力和动向,了解市场需求的变化和趋势,提供决策依据;加强行业科技成果搜集、整理与分析,建立符合产业特点的成熟度评估机制,贯通“科产金”循环,优化和新建机床领域创新成果产业化服务平台、产业大脑、供需平台等成果转化平台,加速推动机床创新成果的迭代升级与应用。
三是加速产品和技术熟化同时建立中试验证标准。在产品和技术熟化、产业化的过程中,需要机构或平台以第三方视角,制定标准,公平公正地评价产品,为高端机床提供迭代升级的“诊断书”,加速产品技术迭代和建立高端用户对国产产品的信任信心。这些平台应具备衔接数控系统及功能部件企业、主机厂、客户、高校科研院所的能力,能够支撑基础共性技术、“杀手锏”技术、应用技术的推广,同时还要拥有专业评估、独立客观公正、综合全面、中试验证标准等服务能力。
目前,依托政府、龙头企业、高校科研院所,国内已搭建了诸多创新中心或中试验证平台。但从发展运行情况来看,大多数平台尚未形成“用户 - 主机厂 - 数控系统及功能部件 - 高校”协同创新的良好生态,也缺乏自我造血的运营能力,未能有效提升高端机床的市场应用信心。
因此,平台仍需持续扶持,汇聚各方优势资源,形成强大的创新合力,成为相关领域高端数控机床的“技术跃迁路由器”,推动我国从机床制造大国迈向机床制造强国。
中试验证案例
▶ 浙江省高档数控机床技术创新中心
浙江省高档数控机床技术创新中心(以下简称:省创中心)于2023年1月由浙江省人民政府批准创建,依托浙江大学、台州市人民政府、温岭市人民政府,联合国企、高校技术团队以及11家民营企业共同建设,是浙江实施创新驱动发展战略、探索新型举国体制浙江路径的高能级科技创新平台,给出了政产研用区域协同技术创新、产品和技术熟化/产业化的浙江答案,现有专兼职人员166人,其中含国家级/省级领军人才10人,台州市人才计划4人,高级职称及博士占比达31.3%,形成“院士团队领衔、青年英才支撑、技能工匠保障”的立体化人才矩阵。
省创中心搭建了高端机床卡脖子技术研发、高档数控机床中试验证、数控机床成果转化、精密制造产业化四个平台,破解工业母机产业链的创新瓶颈、助力产品和技术熟化落地和产业化,同时,建立社会性服务和自我造血生存能力。目前已与北平机床、华中数控、杭机股份、浙江大学等合作承担省部级科研项目23项,其中国家级项目9项,省级项目14项,国拨省拨专项经费共计8434万元,申请发明专利11项、实用新型专利2项,已授权发明专利7项、实用新型专利2项,软件著作权13项;组成32人的数控机床技术应用场景建设专家组,建成华中数控系统应用研发中试基地、超硬刀具研发中试基地;正积极探索适配产线的数控机床中试验证平台,已联合杰克、东部数控开展适用于产线的零件加工、数控机床、监控运维等中试验证工作;同时,高端数控机床及关键技术中试验证基地也在同步建设中,并形成海德曼和高档数控机床产品开发两个成果转化模式,推动华中数控系统和主机快速落地企业和产业化。
省创中心正在对标优秀中心,做好以中心引领的教科人一体、科技创新与产业创新深度融合两篇大文章,夯实四大平台,完善创新生态,强化有组织有市场科研和有组织转化有机统一,全速推进省创中心各方面建设,为中试验证和技术创新平台提供浙江答案。
▶ 南京理工大学数控机床功能部件共性技术工业和信息化部重点实验室
数控机床功能部件共性技术工业和信息化部重点实验室(以下简称数控机床功能部件重点实验室)是滚动功能部件测试试验第三方测试平台,平台研发了25 种类测试装备直接提供试验装备产品,服务于生产厂家和产品用户;以统一的标准开展行业产品性能测评,测试水平达到国际先进水平。首次编撰出版《数控机床功能部件优化设计选型手册》,填补国内空白。承担了 38 项国家级科技项目,授权发明专利200余项,出版行业专著 8 本,软件著作权 14 项,发表国际顶级期刊论文 200 余篇,制修订国家及行业标准 24 项。
研究团队依托南京理工大学建设“长三角智能制造装备创新港”,拥有自主研发的以丝杠为代表的滚动功能部件专用检测设备104台套,建设与项目研究密接相关的实验面积总计1.8万平方米,拥有滚动功能部件和刀库部件成套测评方法、装备和技术。与日本THK、东京精密、德国Rexroth、德国IPA研究所、德国ISW研究所、英国Taylor Hobson、韩国KIMM研究所等国际先进水平相比,检测内容更为全面,测试精度和效率更高,整体达到国际先进水平。具体为:
(1)以功能部件设计与试验共性技术为主体的重点实验室(张家港-基础理论、设计与试验技术前沿研究);
(2)滚动功能部件产业化工程试验基地(连云港-工艺与制造共性技术、产品中试);
(3)滚动功能部件创新综合体(丽水-检测中心、技术与服务辐射);
(4)长三角智能制造与装备创新港高端机床装备技术创新中心(汤山-滚道高精磨削与工艺融合创新研究);建设成“四基地”的实验室体系。为本项目从科学问题研究、工程技术突破、到成果验证应用提供了强有力的保障。
数控机床功能部件重点实验室依托5个牵头的国家级科技项目,历经十余年,聚焦滚动功能部件可靠性、精度、刚度、预紧力4类核心指标,研发了服役性能成套测试装备共计25种,形成了一整套科学完善的性能测评方法体系,解决了标准不统一的行业共性难题,攻克了丝杠高精研磨改性和高效旋铣等性能提升关键工艺技术,提出了高刚性设计方法和预紧力可控的高精装配方法。从“测”、“评”、“标”、“提”四方面大幅提升产品检测和制造水平。形成的成套测试装备、测评方法与标准等技术发明成果,在包括国家级质检单位和滚动功能部件骨干企业在内的23家单位推广应用,累计销售70余台套,市场占有率60%以上;以统一的标准开展行业产品性能测评;组织境内外滚动功能部件产品的性能检测和质量评价工作,对高档数控机床滚动功能部件骨干企业与境外企业的产品进行批量的刚度、综合性能和精度保持性试验,并将测评结果向社会公开,有效推动国产滚动功能部件的服役性能大幅提升,产品国际竞争力显著增强,在中高档数控机床和国防军工高端装备中替代进口、大批量配套应用,助力境内企业滚动功能部件产品在中高端市场占有率从5%提升至20%。
数控机床功能部件重点实验室聚焦滚动功能部件可靠性、精度、刚度、预紧力等关键指标研究,形成成套测试装备、测评方法与标准等完整中试评测链,以第三方检测视角服务于国产滚动功能部件评测,提振国产滚动功能部件高端应用信心。
来源:中国工业报