目前,能查到的能够实现大型复材构件3D打印的设备制造商有三家。cincinnati、ingersoll、thermwood,都是美国公司,实力强大。
第一家,Cincinnati。老牌数控机床、自动铺带/铺丝设备供应商。故事起源于一辆复古小车的制造——3D打印车身。
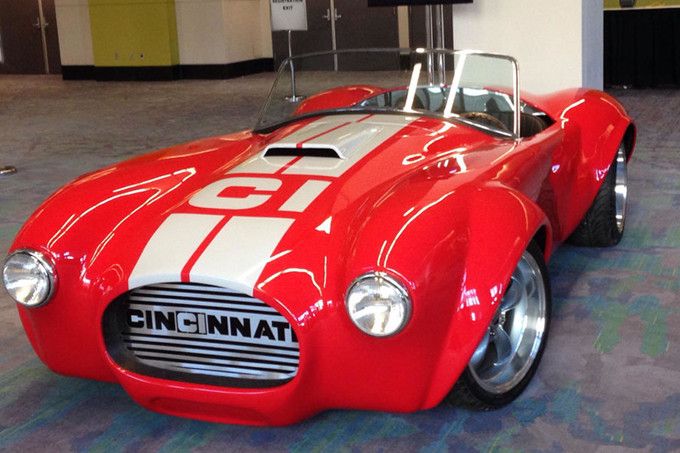
该辆3D打印超跑,由美国能源部设在ORNL(橡树岭国家实验室)里的增材制造展示中心,通过Cincinnati的BAAM(大面积增材制造)机器打印制成。
小型潜艇的尝试
橡树岭国家实验室(ORNL)与美国海军的颠覆性技术实验室(Disruptive Technology Lab)合作,开发出美军的第一个3D打印潜艇船体。这个30英尺长的碳纤维示范船体是用ORNL的大面积增材制造(BAAM)3D打印机打印的,一共只花了几天的时间。
潜艇建造是一件烧钱的事,平均的船体成本在60万到80万美元之间。为此,美国海军一直在不断寻找新方法来降低成本。通过最近与ORNL的合作,现在,他们成功将潜艇的成本降低了90%。新的3D打印船体是一个可选的载人技术示范船体,受到传统的SDV的启发,但不同于之前的任何潜水器。这个30英尺的结构由一种碳纤维复合材料制成,主要包含六个部件。令人难以置信的是,从概念到组装,整个过程花了不到四个星期。
美国海军并未透露太多如何3D打印潜艇的信息,但它和ORNL都表示将利用在这个项目上获得的经验来进一步开发类似的3D打印技术。
风机叶片模具的尝试
在温室效应日益加剧的当下,人类比以往任何时候都更加渴望清洁能源——风能、水电和太阳能等。但是成本问题始终是挡在人们面前的一大障碍,为此,隶属于美国能源部的先进制造办公室(AMO)转向了3D打印技术以减少风力涡轮机的开发成本。由于风力涡轮叶片的长度动辄超过40英尺,AMO为此打算先分成6英尺长的部件分别3D打印出来,然后组合成模具,使其可以浇铸出完整的叶片。
具体来说,这个巨型的3D打印风电叶片模具是由风电&水电技术办公室(WWPTO)、美国橡树岭国家实验室(ORNL)、美国桑迪亚国家实验室(SNL)和企业合作伙伴TPI Composites共同合作开发的,并试图将一种全新、清洁的制作方法带给风电产业。这个项目正好在2016年6月15日的世界风能日完成。
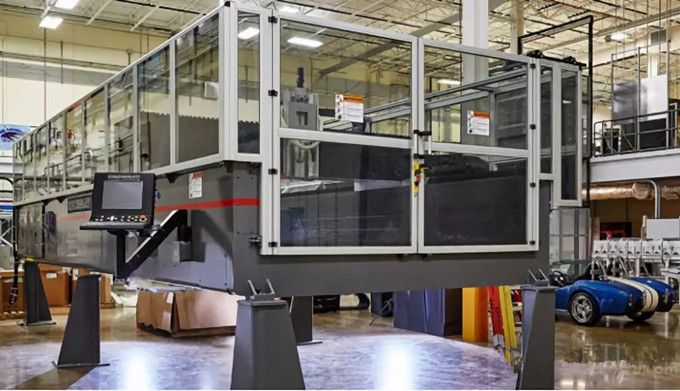
当然你可能会问:这种3D打印的风电叶片模具有什么好处呢?据AMO团队解释说,这个项目引入3D打印技术是为了降低原型和制造下一代风力涡轮机所需的成本和能源。“我们可以通过制造清洁能源技术提高我们国家的竞争力。3D打印技术的优势在于它能够减少浪费、缩短生产周期,并为设计带来更多的灵活性。而且随着技术的发展,3D打印系统的能力也不断提升。”他们认为。不过,像这种巨大的涡轮叶片同样需要超大的3D打印机,幸运的是ORNL的制造示范中心(MDF)提供了大幅面增材制造(BAAM)3D打印机。这款3D打印机比市场上大多数的工业3D打印机速度快500到1000倍,它的打印尺寸也是其它竞争对手的数倍以上。在这里,打印尺寸是相当重要的,因为一个完整的研究叶片就足有42英尺长(约合13米)。如此长的叶片,即使是BAAM3D打印机也不能一次打印出来。为此,开发团队做了一下变通。首先,研究人员开发出了该研究叶片的一个CAD模型,这个模型基本上是一个典型的叶片设计,可以被倒进模子里的那种;然后人们将其分割成割可3D打印的部分,并加上装配孔和加热空气管道系统的设计。
一旦完成了这些工作,他们会在叶片上面覆盖一层玻璃纤维层压板,并进行光滑处理。“每个模具段都被安装在一个框架上,并配备一个热空气鼓风机、温度控制器和热电偶。这个创新的空气加热技术可以节省能源,并消除了用人工铺设嵌入模具的电热丝这一非常麻烦的步骤。而且,这种空气鼓风机在以后的模具中也可以再次使用。”AMO的研究人员说。一旦组装完成,这巨大的3D打印模具就具有非常平整、光滑的表面,而且具有气密性,非常适合铸造风力叶片——而且比传统的风力叶片便宜得多。据研究人员们称,他们的几个研究叶片都是用这个3D打印的模具制造的。
ingersoll的努力
ingersoll作为老牌装备制造企业,在复合材料3D打印技术上也在寻求突破,俺不服,干就完了。
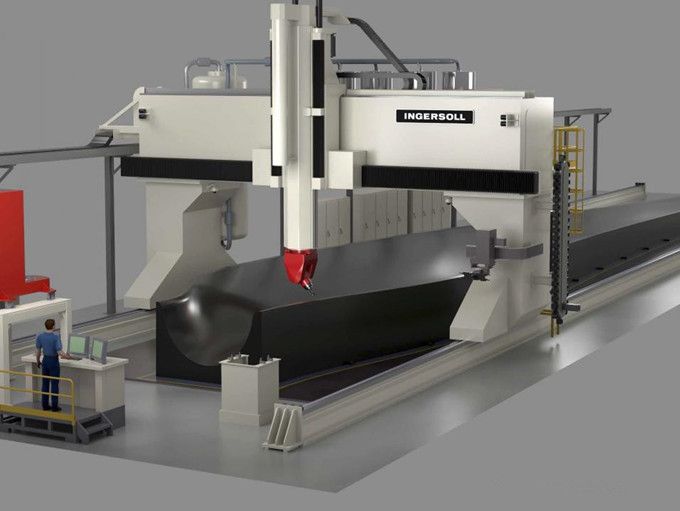
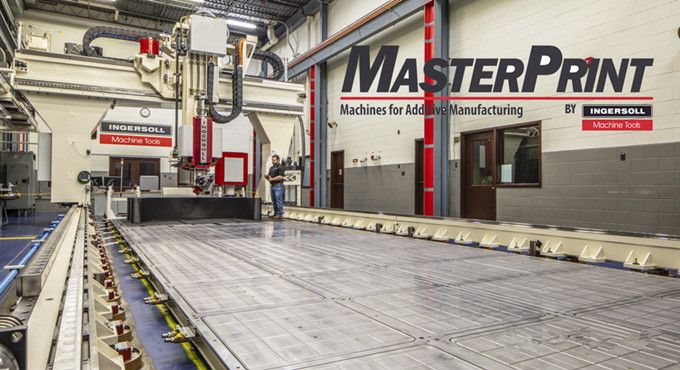
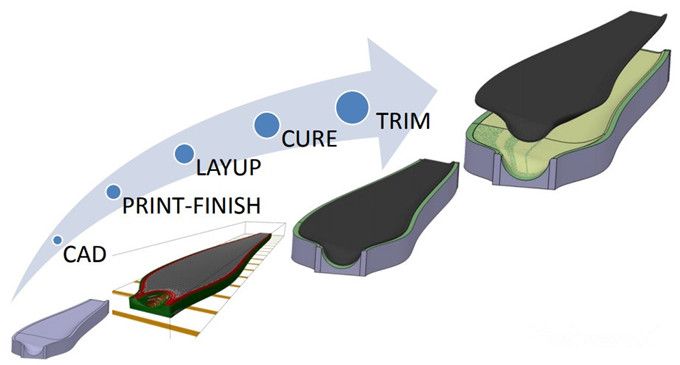
Thermwood,实力不凡
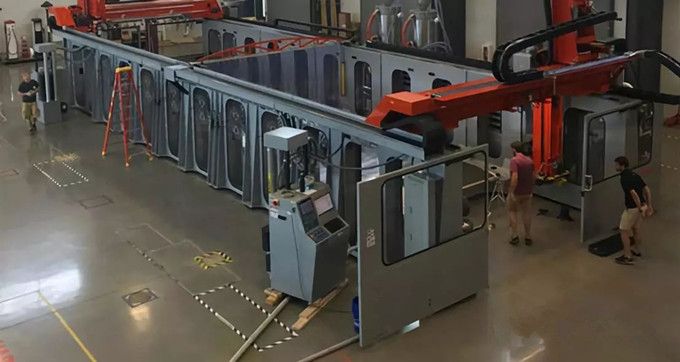
LSAM 3D打印使用Techmer PM的工业颗粒,其比例为80%ABS塑料和20%碳纤维。为了提高零件的刚性,公司计划在未来进一步提高热塑性碳纤维的比例。
波音和Thermwood 公司已采用增材制造技术为 777X 计划生产大型单件工装。该项目表明,增材制造已准备好为航空航天业生产高质量的工装。Thermwood使用大规模增材制造(LSAM)机器和新开发的垂直层印刷(VLP)3D打印技术将该工装一体式成型,从而消除了组装多个3D打印工具组件所需的额外成本和时间。在联合演示计划中,Thermwood在印第安纳州南部的示范实验室打印并加工了 12 英尺长的研发工装,并于 2018 年 8 月将其交付给波音公司。波音研究与技术工程师 Michael Matlack 认为,Thermwood的增材制造技术在此应用中提供了一个显著的优势,可以节省数周的时间。波音公司为位于华盛顿州埃弗雷特的室内设计责任中心(IRC)工厂购买了具有 VLP 功能的Thermwood LSAM 机器。能够适合现实生产环境的质量水平快速生产大型工装,这是推动这项技术从实验室转移到工厂车间的重要一步。
贝尔直升机叶片工装打印。在收到模型和需求后,Thermwood团队迅速行动起来。利用他们新的60毫米熔体核心技术,他们开始使用TechmerPM的25%碳纤维增强PESU(聚醚砜)连续打印工具。Techmer与Thermwood紧密合作,专门为LSAM添加剂印刷制定了这种材料。该可打印材料的玻璃化转变温度超过400°F,在90 psi时,可以很容易地经受普通航空航天部件高达360°F的固化循环。
Techmer的新材料和Thermwood的印刷技术结合在一起,使打印时间仅为3小时8分钟,打印时间减半,“打印”重量为542磅。
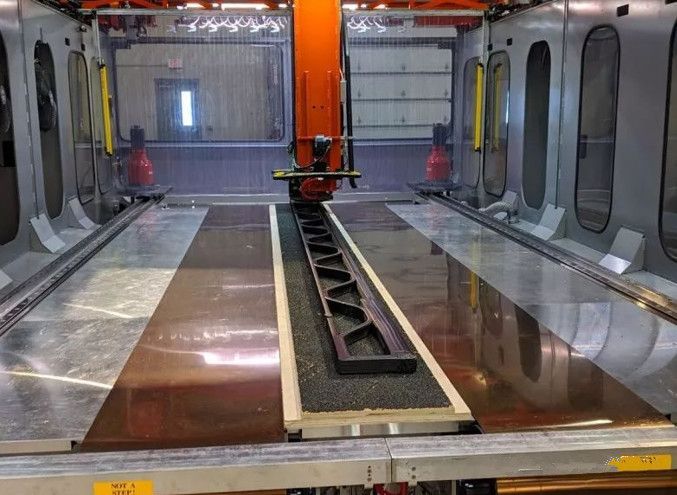
大型复材构件3D打印,在汽车、船舶、轨道交通等领域应用可能还行,航空航天对复材结构的减重和强度要求较高,纤维的连续性至关重要,这种3D打印技术可能很难直接应用,不过,作为复材模具制造的工艺,是一个不错的选择。
来源:先进航空制造技术